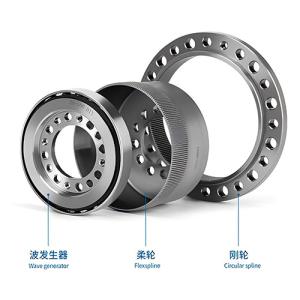
Add to Cart
High Performance Harmonic Drive Reducers Core Components JimaFor develops customised harmonic gearboxes with international robot manufacturer. The company allocates 30% of its annual sales revenue to the research and development of new customized products. Our products are exported to regions with advanced robotics technology, such as Europe, the United States, Japan, and South Korea, as well as emerging markets like Southeast Asia and the Middle East, where the demand for service robots is growing rapidly. Our Advantages 1. We provide high-cost-performance, high-reliability, and lightweight harmonic reducers and core components (such as flexsplines, circular splines, and wave generators) specifically designed for humanoid robots. 2. Cost Advantage: With a mature industrial chain in China, we can control raw material and labor costs, enabling us to offer products at 20%-30% lower prices than international brands. This addresses issues such as high costs and long delivery cycles. 3. Technological Iteration Capability: Leveraging collaboration resources with domestic universities (e.g., Tsinghua University, Harbin Institute of Technology), we accelerate our R&D cycle. 4. Continuous Investment in R&D: We focus on improving the lifespan of flexspline materials and upgrading precision machining equipment. 5. Rapid Sample Delivery: We commit to delivering customized sample orders within 15-20 days. 6. Achieving High Precision and Long Lifespan: Through precision machining processes (e.g., gear grinding, heat treatment) and assembly techniques, we resolve issues such as gear slippage and insufficient rigidity, meeting the high-frequency motion demands of humanoid robots. Our products feature large transmission LC, high load capacity, compact size, lightweight, high transmission efficiency, long lifespan, smooth operation with minimal noise and no impact. Collaborative Case Project Tesla Humanoid Robot Dedicated Harmonic Drive Core Component - Flexspline Challenges: Structural Challenges: 1. The flexspline wall is thin (typically only 0.1-0.3mm thick), making it prone to deformation or vibration due to stress concentration during processing, which affects precision. 2. Extremely high tolerance precision requirements (micrometer level) make it difficult to control tooth profile modification and meshing stability, leading to potential slippage or resonance phenomena. Material Challenges: Traditional materials (e.g., 40CrNiMoA) rely on imports, resulting in high costs and susceptibility to fatigue fracture. Their lifespan struggles to meet the high-frequency motion demands of humanoid robots. Process Challenges: Processing requires multiple complex steps (e.g., forging, gear hobbing, heat treatment), particularly the support of the flexspline inner wall and cutter displacement control, which rely on highly skilled technicians, leading to low mass production efficiency. Our Solutions: 1. Material Innovation: Breaking import dependency and enhancing lifespan Domestic material substitution: Domestic 40CrNiMoA reduces costs by 70% and shortens production cycles by three times. 2. Process Optimization: Precision manufacturing and automation upgrades > New processing methods: Improved flexspline forging and gear hobbing parameters, combined with AI simulation for optimized deformation control, reduce processing errors and increase yield by 30%. > Automated assembly: Smart manufacturing lines utilize machine vision and force control technologies to replace manual assembly, addressing meshing precision issues between the flexspline and circular spline.